Plan your routes effectively
Monitor the real-time stock, technical and encashment data, and visit machines only when necessary with the right products and tools.
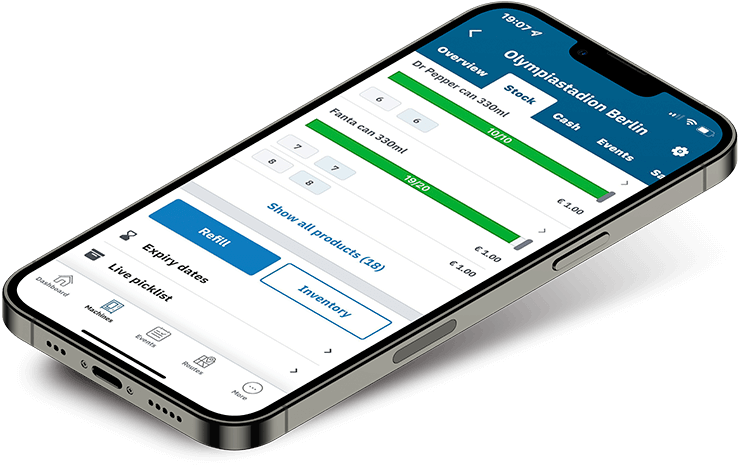

Optimize routes and save money
Planning your routes by pure luck can make you lose up to 120 EUR per visit

Unnecessary vending and coffee machine visits significantly increase the costs of logistics operations.
Operators can save up to 40% on routing costs by planning trips beforehand and visiting only those machines that require filling or repair.
Plan your routes more effectively
Vendon Cloud ensures that operators have access to real-time stock, technical, and encashment data.

Vendon Route planning solution helps to identify different scenarios, ensuring your employee visits a machine with the right tools for each situation:
For product refill
with the right amount of products
For technical maintenance
with the appropriate working tools
For encashment
with the correct amount of cash

Main features of the route planning and pre-kitting solution
Accountability
Since all completed actions for each vending or coffee machine must be registered, our solution allows operators to track progress in the system.
Scheduled picklist update
Update the stock values just before picking, thus minimizing the difference between products picked and products missing in the machine.
Tasklist
Add additional miscellaneous tasks to each machine, such as washing the window, disinfecting the buttons, replacing products, writing down the counters, or anything else that is needed, to ensure that each machine is fully serviced in one trip and doesn't require any additional visits.
Pre-kitting
For simpler warehouse navigation we’ve made pack lists that also include the location of each stock item in the warehouse, defined by the operator. This speeds up the picking process and eliminates situations where employees don’t know the way around the warehouse and spend a lot of time locating items that are on the pack list.
Service routes
Make standalone routes to plan maintenance visits easily. Be it a quarterly checkup, clean-up before the holiday season closures, or an emergency visit — every task can be mapped to machines independently of the refills or cash collections. This ensures no tasks are forgotten, and all information is stored electronically.
Location sequence change
Change the sequence of location visits using the drag-and-drop functionality to create an ordered list of locations that match the situation. All changes are synced with the mobile app in real time, so the employees doing the rounds always have access to the latest information.
Inventory changes
Make any product adjustments and provide the reason for changes — whenever a product quantity is updated outside of a regular refill (by automatic or picklist values), any user can see the reason for the change. This information can be used to analyze the most frequent culprits, and improve business processes.
Mobile app support
Vendon Mobile offers full route management support — from picklists and coin changer refill values to additional tasks and navigation. All actions can be confirmed on the app, which is instantly synchronized with the Cloud solution. That way, the need for paper printouts and manual system updates is kept at a minimum, and route accuracy is improved.
What are the benefits of the route planning and pre-kitting solution?
